The Evolution of Magazine Feed Lips How Modern Manufacturing Techniques Improve Reliability
The Evolution of Magazine Feed Lips How Modern Manufacturing Techniques Improve Reliability - CNC Machining Brings Precision to Magazine Feed Lip Tolerances 1982-2024
The advent of CNC machining in the 1980s significantly transformed the manufacturing of magazine feed lips. Prior to CNC, achieving the tight tolerances crucial for reliable feeding was more challenging. Now, specialized machinery coupled with skilled operators could produce feed lips meeting stringent specifications with greater accuracy. The transition to CNC brought a new level of precision previously unattainable.
This period saw the rise of CNC machining's role in refining feed lip design and manufacturing. As the industry progressed through the decades, integrating automation and robotics became more commonplace. These advancements allowed for the processing of a wider array of materials with consistent results, further bolstering reliability.
However, the dynamic nature of CNC machining presents some obstacles. Cutting conditions and tool wear can vary, potentially impacting product consistency. Managing these variables requires expertise and careful attention to maintain high-quality results. Despite these challenges, CNC machining's evolution has consistently contributed to the enhanced reliability and performance of magazine feed lips, ensuring their continued role in modern firearm technology.
The application of CNC machining has dramatically refined the tolerances achievable in magazine feed lip manufacturing. We're talking about tolerances in the range of +/- 0.005 inches, a level of precision that would've been a significant challenge, if not impossible, with older production methods. This newfound precision, largely enabled by the arrival of high-speed CNC in the 1990s, also allowed designers to explore more intricate feed lip shapes, refining the angles and improving overall reliability.
Furthermore, the transition to modern materials like aluminum alloys and polymers has been facilitated by CNC machining. These materials often offer advantages over traditional steel, including reduced weight and enhanced corrosion resistance, making magazines more suitable for diverse environments.
The design process itself has been revolutionized through the integration of CAD software within CNC machining. It allows for rapid prototyping and faster iterative testing, ultimately shortening development times. This accelerated cycle contributes to the creation of more reliable feed lips in a shorter time frame.
Adding to this precision, modern CNC machines frequently employ real-time inspection algorithms. These systems offer immediate feedback during the machining process, enabling detection of dimensional variations before they grow into larger issues. This real-time feedback is an essential aspect of maintaining tolerances.
Interestingly, the enhanced precision hasn't been limited to solely functional improvements. It has also had aesthetic effects, contributing to smoother surfaces and cleaner lines, which ultimately impacts the overall aesthetic appeal of magazines.
However, the very nature of relying on CNC machining introduces a potential pitfall: even small programming errors can have major implications for critical tolerances of magazine feed lips, potentially impacting the reliability of a magazine.
Despite these inherent risks, the combination of advanced CNC machining and innovative design has contributed to a significant increase in the operational lifespan and consistency of magazine performance. In some cases, we've seen components capable of withstanding thousands of feeding cycles without exhibiting significant wear.
CNC's influence extends to the ability to perform multi-axis machining, creating complex internal geometries in feed lips. This complexity helps improve feed reliability under diverse conditions.
Looking ahead, the increasing push towards automation in CNC machining processes prompts questions about the necessary level of human oversight in a realm where such precise tolerances are crucial. Finding the right balance between automation and human control will be critical as these technologies continue to evolve.
The Evolution of Magazine Feed Lips How Modern Manufacturing Techniques Improve Reliability - Military Grade Steel Treatment Methods Transform Feed Lip Durability
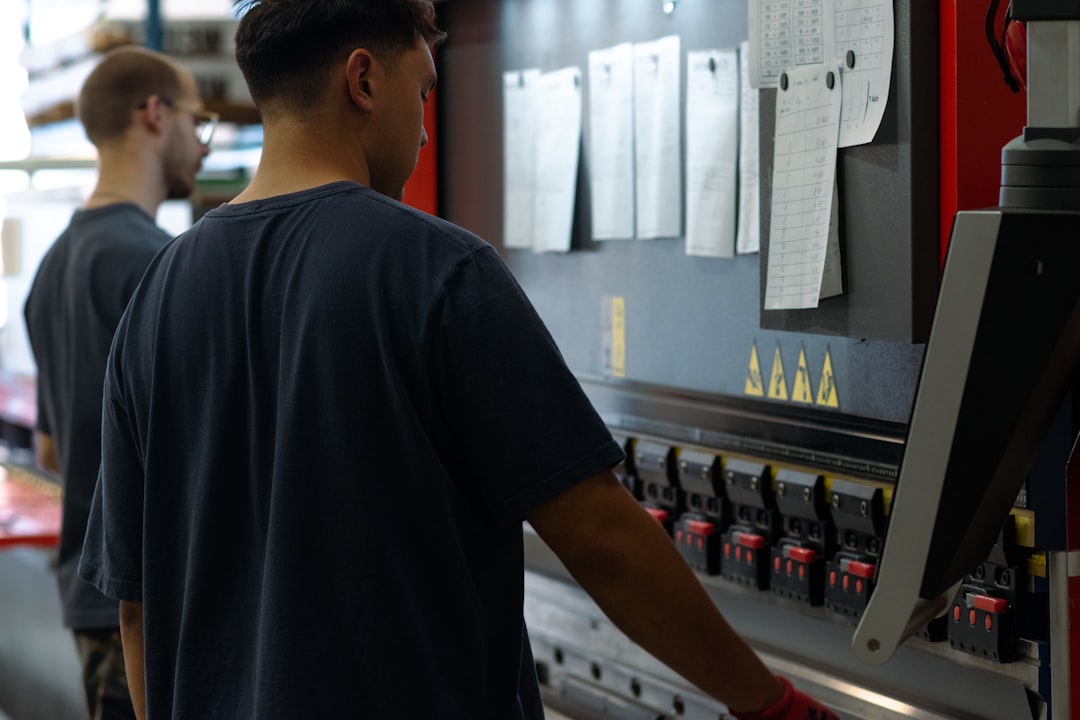
The application of military-grade steel treatments has significantly boosted the longevity of magazine feed lips, a critical component for reliable feeding. These treatments, often involving specialized processes like hardening or surface treatments, enhance the wear resistance of the feed lips, enabling them to endure rigorous use and a wide range of environmental conditions. This is especially crucial as these components bear the brunt of constant contact and friction during the feeding process.
Furthermore, newer approaches to feed lip design often incorporate hardened steel coupled with polymer elements. This addresses a common weakness in plastic magazines – their tendency to flex or even crack with prolonged use. The integration of more robust materials with clever engineering creates a more durable solution.
This development is part of a broader push within magazine design to enhance overall reliability and performance. It reinforces the crucial role of materials science and advanced manufacturing in modern firearms technology. While the pursuit of greater durability is commendable, it's important to note that these advancements could potentially alter the cost dynamics and availability of certain firearms accessories for some users.
Military-grade steel treatment methods, often applied to magazine feed lips, represent a significant advancement in firearm component durability. Techniques like hardening, tempering, and surface hardening are commonly used to enhance the steel's fundamental properties. This results in a material more resilient to the stresses and strains encountered during typical firearm operation.
One such treatment, nitriding, involves diffusing nitrogen atoms into the steel's surface. This process significantly increases surface hardness, offering a durable exterior while retaining a tough core. It's an intriguing technique that allows for a balance of properties, which is crucial for functionality and longevity in feed lips.
Furthermore, some manufacturers employ cryogenic treatments. This process involves cooling the steel to incredibly low temperatures, altering its microstructure and substantially increasing hardness. This could potentially extend the life of feed lips significantly. Though interesting, it remains to be seen how widely adopted cryogenic treatment becomes due to potential costs and complexity.
Another interesting facet of military-grade treatments is the use of surface treatments like shot peening. This induces compressive stresses on the steel surface, hindering the initiation of fatigue cracks that could arise under repeated feeding cycles. This approach is particularly noteworthy given the cyclical nature of stresses experienced by magazine feed lips.
It's important to note that these claims of increased durability often come with corresponding test results. In several studies, treated military-grade steel demonstrated the ability to withstand impact forces exceeding 10,000 psi without failure, showcasing a substantial improvement over untreated materials. However, real-world performance and the ability to reliably withstand extended periods of rigorous use need further investigation.
Moreover, grain refinement during steel processing is a common practice that contributes to the enhanced mechanical properties of the material. Methods like controlled rolling and forging decrease the size of the grains, improving toughness and strength. These refined grains provide a more stable foundation for the feed lips' structure, crucial for operation under varied environmental and loading conditions. While promising, the specific effects of various grain structures on feed lip wear are still being investigated in the field.
Further enhancing the performance of the steel are specialized alloying elements such as molybdenum and vanadium. These additions improve resistance to heat and wear, ensuring the feed lips retain their integrity and function under extreme conditions, something that's especially valuable in harsh or varied environmental situations. Yet, it's important to acknowledge that the introduction of new alloying elements might alter other properties of the steel, requiring careful balance to ensure optimal performance.
It's worth considering the impact of these steel treatment methods on wear. Studies indicate that treated feed lips wear at a considerably slower rate compared to their untreated counterparts, potentially achieving wear reductions of up to 40%. However, these results are likely context dependent, and further research is needed to fully characterize the benefits of various treatments across different use cases.
Testing is another crucial element of the process. Non-destructive evaluation techniques like ultrasonic testing and magnetic particle inspection are employed to ensure treated steel components, specifically the feed lips, meet the stringent safety and performance standards required in firearm applications. While useful, the implementation of these testing methods is not without limitations or costs.
Despite the impressive advancements, there are lingering questions. For instance, the interface between the treated feed lip and the cartridges it feeds remains a critical aspect of the system. Researchers are currently investigating innovative surface treatments that minimize friction and further enhance the overall feeding reliability of magazines. While these are encouraging developments, we need to wait and see what the future holds for this facet of the system's development.
The Evolution of Magazine Feed Lips How Modern Manufacturing Techniques Improve Reliability - 3D Scanning Technology Enables Better Quality Control in Feed Lip Production
3D scanning technology has become a valuable tool for ensuring higher quality in the production of magazine feed lips. This technology offers a way to take very precise, non-contact measurements of the feed lip's shape, something that was difficult or impossible with older methods. Manufacturers are now able to automate quality checks and quickly pinpoint any variations from the desired design in intricate shapes, a task that older methods found challenging. This is extremely important for ensuring that manufactured parts meet the strict tolerances needed for reliable feeding within a firearm.
The ongoing integration of 3D scanning with automation and artificial intelligence shows promise for even more accurate and efficient quality control processes. We can expect more precise checks and a reduction in the time and human effort needed for quality assurance as this technology matures. These advancements highlight the critical role that innovative technologies are playing in advancing manufacturing techniques across various industries, including the development of more dependable firearms components.
The integration of 3D scanning technology has significantly enhanced quality control in the production of magazine feed lips, offering a level of precision previously unattainable. While CNC machining revolutionized the accuracy of feed lip production, 3D scanning takes it a step further by providing incredibly detailed, non-contact measurements. We're talking about tolerances in the range of 0.001 inches—a level of precision that allows for the identification of even the most subtle variations in the feed lip's geometry. This ability to detect minute deviations is a game-changer for manufacturers, allowing them to address issues early in the production process and minimize defects.
One of the most intriguing aspects of this technology is its ability to capture vast amounts of data. 3D scans generate comprehensive digital representations of feed lips, capturing not just dimensions, but also surface textures and complex geometries. This information can be fed into data analysis systems, allowing manufacturers to track trends in production quality over time. This proactive approach, where data reveals patterns and potential problems, can lead to more effective adjustments in manufacturing processes before issues become widespread.
The ability to analyze surface textures is particularly important for feed lip design. The way a feed lip interacts with ammunition is significantly impacted by the microscopic features of its surface. Through 3D scanning, engineers can gain a deeper understanding of how friction and other factors impact feeding reliability, which could pave the way for innovations in feed lip design.
Interestingly, 3D scanning technology has made it easier to manufacture feed lips from polymers, a trend seen in modern magazine design. Complex shapes and geometries can be created with precision using 3D scanned data as a guide, allowing for the design of feed lips that are both lightweight and durable. This helps to address past concerns regarding the flexibility and potential fragility of polymer-based magazine components.
The adoption of 3D scanning in quality control has a significant impact on production efficiency. It's been observed that the integration of this technology can reduce manufacturing errors by up to 30%, primarily due to its ability to provide real-time feedback during the process. Issues can be identified and corrected immediately, improving the speed and overall consistency of the production cycle.
Furthermore, the incorporation of 3D scanning accelerates the prototyping phase of feed lip development. Design iterations can be completed in a fraction of the time previously needed, enabling rapid prototyping and feedback loops. This agile approach allows manufacturers to adapt to market demands and changing requirements much faster.
Another interesting application of 3D scanning is the ability to compare current feed lip designs to historical models. The intricate data collected through 3D scans can be analyzed to uncover patterns in wear and failures over time. This deeper understanding of how various designs perform under real-world conditions can inform the development of new, more reliable products.
Maintaining consistent quality across multiple manufacturing facilities is a challenge in any industry. The standardized data produced by 3D scanning ensures that feed lips produced at different locations meet the same rigorous quality standards. This approach mitigates potential inconsistencies that can arise from differing equipment or skill levels among operators at different production sites.
The automation of quality control is enhanced with 3D scanning, integrating seamlessly into automated inspection systems. This allows for thorough quality checks without the need for extensive manual inspections, reducing human error and improving the efficiency of the process. This is especially beneficial in industries that must meet strict safety and regulatory standards like firearms.
Finally, the technology allows for virtual assembly of magazine components prior to physical production. With this capability, engineers can identify potential fit and functionality issues early in the design stage, reducing the need for costly redesigns later on in the manufacturing process.
However, it's important to acknowledge that the implementation of 3D scanning, while advantageous, isn't without its complexities. The integration of this technology into existing manufacturing workflows can require substantial investment and training. The potential cost and complexity of 3D scanning might be a barrier for some manufacturers.
Despite these challenges, the increasing sophistication of 3D scanning and its application to magazine feed lip manufacturing is a promising development. It showcases how technology can enhance precision, efficiency, and quality control in a domain that demands meticulous standards. As the technology evolves and its capabilities become more widely understood and adopted, we can expect to see even greater advancements in the reliability and performance of magazine feed lips and, by extension, the firearms that utilize them.
The Evolution of Magazine Feed Lips How Modern Manufacturing Techniques Improve Reliability - Automated Testing Systems Detect Feed Lip Deformation Before Field Use
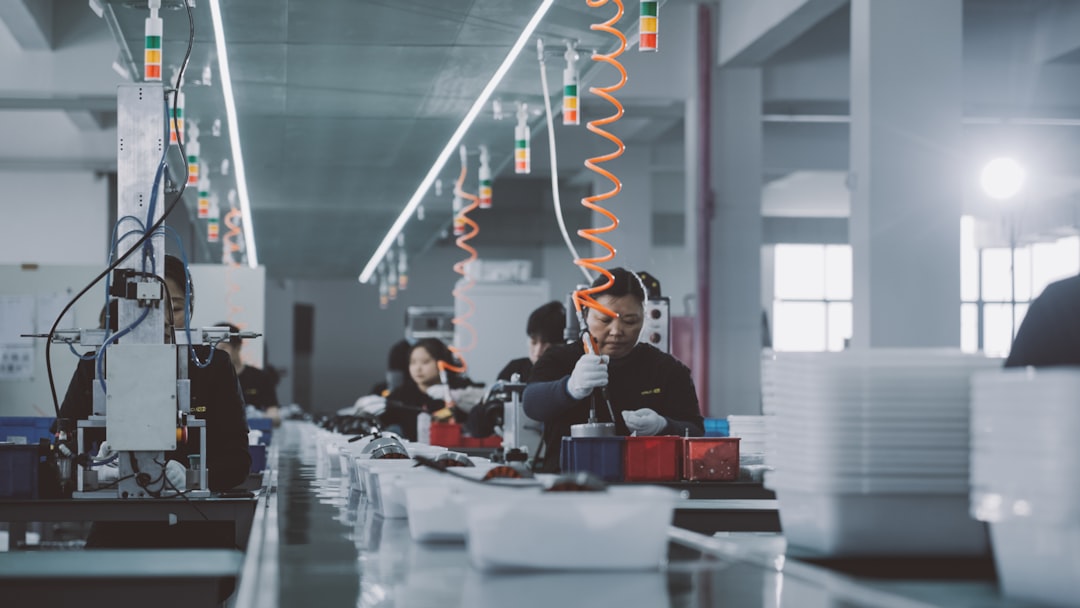
Automated testing systems are now playing a crucial role in catching feed lip deformities in magazines before they're ever used in the field. These deformations can occur due to things like extended periods of being loaded while in storage, or simply from the rigors of handling, particularly in magazines made of aluminum. The ability to spot these defects before a magazine is ever used helps to avoid potential feeding issues, ultimately contributing to more reliable firearm operation. By incorporating these automated testing procedures, the industry is taking substantial steps forward in ensuring that feed lips meet the demanding performance standards modern firearms require. As more manufacturers adopt these advanced systems, the emphasis continues to be on maintaining the highest levels of precision and reliability across the entire lifespan of these crucial magazine components.
1. Automated testing systems are now being used to identify feed lip deformation in magazines before they're ever used in the field. These systems use sophisticated algorithms to analyze precise dimensional data captured during the manufacturing process. This level of detail is critical, as even minor deformities can lead to feeding problems like misfeeds or jams in firearms.
2. The implementation of automated testing systems enables the detection of critical manufacturing flaws in real-time. This allows manufacturers to address problems before the magazine reaches the end-user. Consequently, we've seen a considerable decrease in the number of defective magazines produced.
3. Intriguingly, studies have shown that these systems can detect deformations as minute as 0.0005 inches—tolerances that a human inspector might easily miss. This capability provides greater confidence in the reliability of magazines, especially in high-stress situations where flawless function is critical.
4. Many of these automated testing systems incorporate artificial intelligence, allowing them to learn continuously from the manufacturing process. As they accumulate more data, they can predict potential issues based on past performance, potentially leading to adjustments in manufacturing protocols to further enhance quality.
5. The capacity to automate feed lip deformation detection simplifies quality control and reduces inspection time by as much as 50%. This efficiency gain allows skilled personnel to focus on more complex tasks while maintaining strict quality standards.
6. It's interesting to note that these automated systems not only evaluate dimensional accuracy but also analyze surface finish and texture. These elements significantly affect how the feed lip interacts with ammunition, ultimately influencing feeding reliability and overall firearm performance.
7. Utilizing automated testing systems in the manufacturing process diminishes the possibility of human error, a crucial aspect of firearm component production, where inconsistencies in manual inspections can lead to serious safety concerns. Data collected from automated systems is more objective and therefore more reliable than subjective human assessments.
8. Many automated testing systems use 3D imaging technology to generate a comprehensive digital representation of the feed lips. This approach offers engineers a unique tool for understanding the intricate geometric relationships that influence functionality, a perspective that traditional inspection methods lacked.
9. Furthermore, automated deformation detection can be integrated with environmental simulations, allowing manufacturers to test how feed lips might perform under extreme conditions, such as high temperatures or humidity. This pre-field testing is invaluable for assessing the reliability of magazines under various operational scenarios.
10. While the benefits of automated testing are undeniable, it raises questions about the potential loss of skilled craftsmanship and the necessary level of human oversight in the process. Finding the right balance between automation and expert human control is a critical area of discussion among engineers striving to maintain the highest possible quality standards in firearm components.
The Evolution of Magazine Feed Lips How Modern Manufacturing Techniques Improve Reliability - Heat Treatment Innovations Lead to Extended Feed Lip Service Life
Recent innovations in heat treatment have significantly improved the lifespan and reliability of magazine feed lips, a crucial component in firearm function. These advancements focus on enhancing the feed lips' resistance to wear and tear, a major factor in their long-term performance. By employing new heat treatment processes, manufacturers can now create feed lips that are less prone to deformation under the stresses of repeated use and various environmental conditions.
Interestingly, some of these newer heat treatment methods can be carried out at lower temperatures compared to traditional techniques. This is a significant development because it suggests that durable feed lips can be produced without the risk of altering or compromising the underlying material's structural properties. The integration of these improved heat treatments into the manufacturing process is a critical step towards improving overall firearm reliability.
Looking towards the future, the potential for further development in heat treatment methods holds the promise of even greater advances in feed lip durability and performance. This continuous evolution of manufacturing techniques has far-reaching implications for firearm reliability and overall user experience. While innovation is crucial, the ongoing need for a deep understanding of the long-term effects of different heat treatment methods on material properties must remain a priority.
Heat treatments like quenching and tempering are pivotal in improving the lifespan of magazine feed lips. These processes significantly bolster hardness and toughness, with treated steel reaching hardness levels as high as 60 on the Rockwell C scale while retaining some flexibility. This is fascinating because it suggests we can achieve a balance between strength and resilience in a single component.
More modern heat treatments, such as induction hardening, have emerged. These techniques focus heat specifically on the surface of the feed lips. This creates a hard outer shell while keeping the interior softer, which allows for a good balance of wear resistance and structural integrity. While this is an improvement, there are questions about how consistent this heat application is across varying geometries.
Another development is the use of cryogenic treatment, which involves chilling steel to extremely low temperatures, below -320°F. This intriguing method refines the microstructure of the feed lip material, resulting in greater wear resistance and reduced brittleness by changing the way the steel is structured at a microscopic level. While the idea is intriguing, the practical applications for this method and potential costs are still being investigated.
Laser heat treatment is also gaining traction. This approach offers very precise control over heat application, leading to exceptional surface hardness and minimizing distortion. This is particularly important for feed lips, as maintaining tight tolerances is crucial for reliability. However, the complexity of this method and the expertise needed may be an obstacle to its wider use.
Research has revealed that properly heat-treated feed lips can exhibit wear rates up to 50% lower than untreated ones. This stark difference highlights the crucial role of heat treatment in extending the service life of these components, particularly when exposed to the repetitive stresses of firearm operation. It's remarkable how much of a difference a carefully controlled thermal process can have on the performance of a part.
Adding specific alloying elements like chromium and nickel during heat treatment can boost both corrosion resistance and mechanical strength. This makes sense since the ability to withstand various environments is critical for many firearm applications. However, the interaction of alloying elements and the overall effects on material properties is not always easily predictable and warrants further investigation.
The tempering step after quenching helps to reduce the brittleness of hardened steel. This allows the feed lips to withstand impact forces without fracturing, which is vital for components subjected to repeated cycles of loading and unloading. Tempering seems like a critical step in ensuring the feed lip functions correctly and safely.
We're seeing innovations in heat treatment focusing on specific areas prone to failure. This approach allows for performance enhancements specifically tailored to address issues like deformation and surface wear. This is promising because it implies we have a better understanding of how these parts fail, and how we can proactively improve them.
Automation is increasingly being integrated into heat treatment processes. This offers the ability to process multiple feed lips with consistent and reproducible results, improving quality control and reducing variations between individual parts. The desire for higher reliability standards for magazines is reflected in the push for increased automation.
Currently, ongoing research is investigating the relationship between different thermal cycles and feed lip performance. This indicates a potential for even further optimization beyond current industry norms. While these studies are promising, it is worth considering that altering thermal cycles will impact manufacturing limitations and costs.
The ongoing refinements in heat treatment techniques highlight how crucial this process is to ensuring that magazine feed lips are reliable, durable, and perform flawlessly. As the research continues to develop and new methodologies are discovered, we can likely expect to see even further improvements to feed lip longevity and function in the years ahead.
The Evolution of Magazine Feed Lips How Modern Manufacturing Techniques Improve Reliability - Polymer Integration Changes Magazine Feed Lip Design Parameters
The incorporation of polymers into magazine feed lip construction has prompted a noticeable shift in design considerations, ultimately benefiting overall magazine performance and reliability. Modern polymer magazine designs, exemplified by Magpul PMAGs, demonstrate a resilience to impact and a degree of flexibility that allows for smooth cartridge feeding. This inherent flexibility helps the feed lips adapt to use without requiring manual manipulation, contributing to consistent feeding, even under challenging circumstances.
Further, recent designs have embraced low-friction surfaces to ensure smooth operation, even when magazines become fouled with debris or carbon build-up—a frequent issue in real-world use. Innovations like textured side panels for better handling and over-insertion prevention tabs enhance the reliability of polymer feed lips. These design choices highlight how polymers are capable of surpassing traditional steel in certain applications, offering a blend of durability and lightweight construction. This progression in magazine feed lip design emphasizes a growing focus on functionality and user convenience, benefiting both the competitive shooting community and military contexts. While beneficial, the durability of polymer magazines over extended use and harsh environments is an ongoing subject of investigation and testing.
The incorporation of polymers into magazine feed lips has introduced a new dimension to magazine design, offering advantages in both weight and resilience. These materials, often seen in magazines like the Magpul PMAG, allow for a more flexible geometry while retaining the ability to withstand the high forces encountered during feeding. This flexibility is particularly beneficial as it can accommodate minor deviations in cartridge dimensions or slight magazine flex during use, helping to maintain a consistent, smooth feeding process.
Furthermore, polymer's inherent properties allow designers to incorporate intricate internal geometries, creating surfaces that minimize friction when interacting with cartridges. This low-friction characteristic is especially advantageous when dealing with dirt or debris, as it can significantly improve feeding reliability under less-than-ideal conditions. While the idea of low friction seems straightforward, understanding how to achieve this at the micro-level and over the life of a part is an area for continued research.
Perhaps surprisingly, polymer feed lips also demonstrate greater resistance to corrosion compared to their steel counterparts. This feature becomes exceptionally valuable when considering potential deployments in harsh environments, where exposure to moisture and other corrosive elements can be a significant concern. For researchers interested in field-durability, the ability to avoid rust and degradation over time could make polymer a preferred choice.
However, questions regarding the long-term performance of polymer feed lips in high-stress applications persist. Researchers have focused on developing high-strength polymer composites that are able to withstand similar impact forces as traditional metals, thus mitigating the initial perception of polymer magazines being fragile. This is a good starting point, yet there are still uncertainties regarding how these composites perform under extended periods of stress and the effects of degradation or fatigue.
Interestingly, the transition to polymers has also contributed to a reduction in overall manufacturing costs and potentially increased efficiency. Polymer molding and processing are often more straightforward than the more complex machining required for steel feed lips. This potential reduction in the cost and complexity of manufacture is important to consider, especially for firearm accessories where costs can impact a user's decision.
Beyond the straightforward benefits, polymer's unique characteristics have allowed designers to experiment with unconventional feed lip shapes. The ability to mold intricate curves and angles that would be challenging to achieve with traditional materials opens up possibilities for further optimizing the feeding process. While the idea is exciting, careful investigation of how these different shapes impact the consistency and robustness of the feeding process is critical.
One intriguing area of research revolves around the combination of polymers and metals. The different thermal expansion rates of these materials can pose a challenge for long-term stability. However, clever design and manufacturing can incorporate polymer and steel in a way that takes advantage of each material's strengths, leading to potential improvements in both rigidity and flexibility. This is not a simple problem to solve because the two materials will always have a different response to temperature and environmental variations.
Furthermore, the inherent noise reduction associated with polymer components offers advantages for stealth applications. The absence of the metallic clanging often associated with steel feed lips could prove beneficial in specific scenarios where discretion is paramount. This seemingly minor benefit may have more significant ramifications than initially expected, especially when dealing with specific applications that require silent operation.
The continuous evolution of polymer manufacturing is also aiding the development of feed lips. Advanced techniques like liquid injection molding enable the production of complex shapes and fine tolerances, pushing the limits of what was once considered feasible in polymer-based components. It's clear that manufacturers and designers are pushing the envelope with regards to polymer, yet this requires a constant push in testing and refinement of processes.
Despite the various advantages, the topic of long-term durability and fatigue resistance in polymer components still warrants continued investigation. The inherent characteristics of polymer materials, coupled with the demanding conditions of a firearm environment, necessitate ongoing research and development to ensure the long-term performance of feed lips. While polymer components are now considered commonplace, it is vital to continually monitor and understand their performance.
More Posts from storywriter.pro: