Understanding the Science Behind Paper Coatings 7 Key Differences That Impact Print Quality
Understanding the Science Behind Paper Coatings 7 Key Differences That Impact Print Quality - Starch Based Solutions Create Stronger Paper Surface Bonding
Starch-based solutions are gaining prominence as a means to create stronger bonds within the paper's surface layer, a feature vital for achieving superior print quality. Applying starch not only strengthens the paper's structure but also boosts its resilience against water and abrasion, making it suitable for a wider range of printing techniques. While there's potential in using cationic starch and nanocellulose in coatings, their widespread use in industry lags behind the promising research findings, hinting at a disconnect between lab discoveries and practical implementations. Moreover, ongoing work with combinations like starch-silane and bionanocomposites is showing promise in crafting more sustainable and innovative paper products, potentially resolving some inherent challenges of traditional coating methods. However, starch's limitations—particularly its high viscosity and less-than-ideal film formation— underscore the ongoing need for research to overcome these hurdles and realize its full potential in paper production.
Starch-based coatings, derived from a naturally occurring polysaccharide, offer a unique approach to strengthening the paper surface. Their ability to form robust hydrogen bonds with the cellulose fibers within the paper significantly improves the overall physical integrity of the paper substrate. Interestingly, the viscosity of these starch-based coatings can be precisely controlled, enabling a more consistent and uniform application during the coating process, minimizing unwanted splattering and ensuring a smoother surface for printing. This fine-tuning of viscosity is particularly advantageous in ensuring optimal print quality.
Further, starch demonstrates a distinct advantage over synthetic alternatives in its inherent adhesive properties. This enhanced adhesion is attributed to its molecular structure, which allows for stronger binding with the cellulose fibers found in paper. Moreover, the gelatinization process, a key aspect of starch chemistry, imparts a unique gel-like consistency to the coating. This consistency plays a crucial role in filling the inherent porous nature of paper, thus leading to a more uniform and level surface. The resulting surface is highly desirable for achieving high-quality printing.
However, it's important to note the starch's behavior over time, as it undergoes retrogradation during the aging process. This phenomenon leads to increased robustness and durability of the paper's surface, thus extending the paper's life and allowing it to withstand demanding printing processes. It is fascinating how a change in starch composition, specifically altering the ratio of amylose to amylopectin, directly influences the flow properties of the starch-based coating. This property allows for customized application of the coatings according to specific printing requirements.
Moreover, starch-based solutions contribute to a tangible improvement in paper strength, exhibiting heightened resistance to tearing and folding. This is a valuable feature, especially in applications where durability is paramount while maintaining a high-quality printing output. The addition of starch can also create a synergistic effect when used in conjunction with other coating additives, resulting in enhanced attributes such as gloss and opacity. It's remarkable how this interaction further boosts not only the bonding strength but also the overall aesthetic quality of the paper.
Finally, unlike synthetic counterparts, starch-based coatings demonstrate a unique temperature-responsive behavior in their bonding properties. This ability to tailor the bonding strength based on specific environmental conditions during printing further enhances the printing process and allows for more sophisticated control over the interaction of the coating with the paper.
Understanding the Science Behind Paper Coatings 7 Key Differences That Impact Print Quality - Clay Coatings Add Natural Smoothness Without Extra Calendering
Clay coatings offer a way to achieve a smoother paper surface without the need for extra processing steps like calendering. This approach relies on using clay minerals, primarily kaolin, as a core component in the coating formulation. These clays naturally contribute to a smoother paper finish, potentially simplifying the manufacturing process while preserving desirable paper properties. While calendering is often used to increase gloss and evenness, it can sometimes negatively affect the coating's performance. Recent advances in understanding the structure and composition of coatings have led to a growing interest in clay-based approaches for improving print quality. As the search for improved coating solutions continues, clay coatings appear to be a compelling option due to their ability to provide a naturally smooth surface while remaining practical for industrial use. However, it's important to acknowledge that clay coatings might not always be the best choice for every printing application and further research and development are still needed. The ongoing evolution of coatings technology presents exciting possibilities for future refinements in paper production and printing.
Clay coatings offer a compelling approach to enhancing paper smoothness without relying on the additional step of calendering. This is intriguing because it potentially reduces processing time and energy use in paper mills, especially in high-speed printing operations where calendering downtime can be a bottleneck. It seems that clay particles, when incorporated into the coating, interact with the cellulose fibers in a way that creates a more uniform surface. This smoother, more uniform surface improves ink distribution during printing, leading to better print quality.
The fascinating aspect of clay coatings is that their properties can be tuned by manipulating the particle size and shape of the clay used. For example, smaller, plate-like kaolin clays can specifically influence gloss and brightness, which are vital in many printing applications where a high-quality finish is desired. Furthermore, these coatings contribute to increased paper opacity without a significant increase in paper weight. This means we can potentially achieve the same visual effect with thinner paper, leading to reduced paper consumption and potentially a more environmentally friendly process.
The increased brightness provided by clay coatings can also enhance color vibrancy in print. This is particularly noticeable in offset printing, as the clay particles reflect more light, boosting the perceived intensity of the printed colors. This is especially valuable for materials where strong visual impact is important, such as marketing materials and high-quality publications.
One interesting effect of clay coatings is their influence on ink absorption. The presence of clay seems to facilitate faster ink drying, potentially leading to quicker turnaround times in printing. This efficiency gain is critical in modern printing where speed and throughput are prioritized. Also, clay-coated paper surfaces maintain a consistent pH level, which is important for preventing undesirable color shifts during printing. This chemical stability ensures that the colors printed on the paper align with the intended design specifications, thus minimizing the risk of costly reprints due to color inconsistencies.
However, clay, in its inherent nature, can be brittle. Therefore, when designing clay-based coatings, it's crucial to balance the clay content with other coating materials, like latex, to maintain the desired paper flexibility. This trade-off is important for applications requiring folding or binding, where flexibility is crucial. The interactions between clay particles and water-based inks are quite intriguing. They lead to enhanced ink adhesion and reduced ink bleeding, which are common issues in printing. This results in sharper print edges and clearer text, significantly improving the overall print quality.
Finally, research suggests that clay-based coatings can influence the paper's tactile properties, potentially leading to a softer feel. This aspect might be especially relevant for niche applications like stationery and fine art prints, where the tactile experience can be as important as the visual aspect. This area of research could unlock opportunities to further customize the sensory experience of printed materials. While there's a lot to learn about optimizing these coatings, it's clear that they offer a promising avenue for enhancing paper properties in ways that can benefit both the printer and the end-user.
Understanding the Science Behind Paper Coatings 7 Key Differences That Impact Print Quality - Latex Polymers Provide Water Resistance While Maintaining Print Sharpness
Latex polymers are increasingly used in paper coatings, mainly because they offer a balance between water resistance and print quality. By carefully controlling the formulation and using specific surfactants, latex-based coatings contribute to a stable emulsion, which helps preserve surface properties like gloss and smoothness that are crucial for high-quality printing. A promising area of development within latex polymer coatings is the use of new crosslinking techniques. These methods improve water resistance and make the coatings more durable, offering an environmentally friendly alternative to conventional petroleum-based coatings. It's important to acknowledge the need for continuous evaluation and refinement of these coatings to ensure they deliver consistently high performance while meeting growing environmental standards. Research into latex polymers is expected to continue, exploring new ways to optimize their properties and expand their use in various printing applications, creating a future where print quality and sustainability go hand-in-hand.
Latex polymers offer a fascinating approach to improving paper's properties, particularly in relation to water resistance and print quality. Their ability to form stable emulsions is key to achieving a uniform and even coating, which is critical for maintaining sharp print details. The fact that they can be formulated to provide a balance between water repellency and print sharpness, is intriguing. This balance is achieved by controlling the thickness of the latex coating; a thinner coat prioritizes crispness, while a thicker coat emphasizes water resistance. It's a delicate dance between desired properties.
Furthermore, latex polymers can be engineered to respond to temperature changes, which is advantageous during the printing process itself. This temperature sensitivity might affect adhesion and bonding, potentially contributing to more robust printing outcomes. Interestingly, the incorporation of various additives into latex formulations allows for fine-tuning the resulting coatings, tailoring them for specific printing needs. We can potentially create coatings that are more flexible or possess enhanced adhesion without compromising water resistance or print sharpness.
It's not just about repelling water, though. Latex coatings also help to prevent ink from smudging and bleeding, a crucial aspect in high-speed and high-volume printing. This is likely due to how the latex interacts with the cellulose fibers of the paper, perhaps creating a tighter bond that helps hold the ink in place. As a result, print quality is enhanced, with more vibrant colors and sharper edges.
Interestingly, latex coatings might even enhance the durability of the paper surface compared to other coating types. Their flexibility and resistance to cracking or peeling make them appealing for applications involving folding or bending, like brochures or labels. It's also intriguing that they seem to impact the drying time of inks, potentially due to their hydrophobic nature, which reduces water absorption by the paper, thus speeding up the drying process and reducing the risk of ink bleeding.
Recent research suggests that the structural properties of latex polymers are quite malleable. It is thought that by changing the molecular architecture of the polymer, the elastic properties can be optimized for specific printing processes. This is especially interesting when it comes to high-speed printing, where adaptability and resilience are important. This area of research suggests exciting possibilities for future innovation within the paper industry and print quality.
Understanding the Science Behind Paper Coatings 7 Key Differences That Impact Print Quality - Titanium Dioxide Additives Enhance Paper Whiteness and Opacity
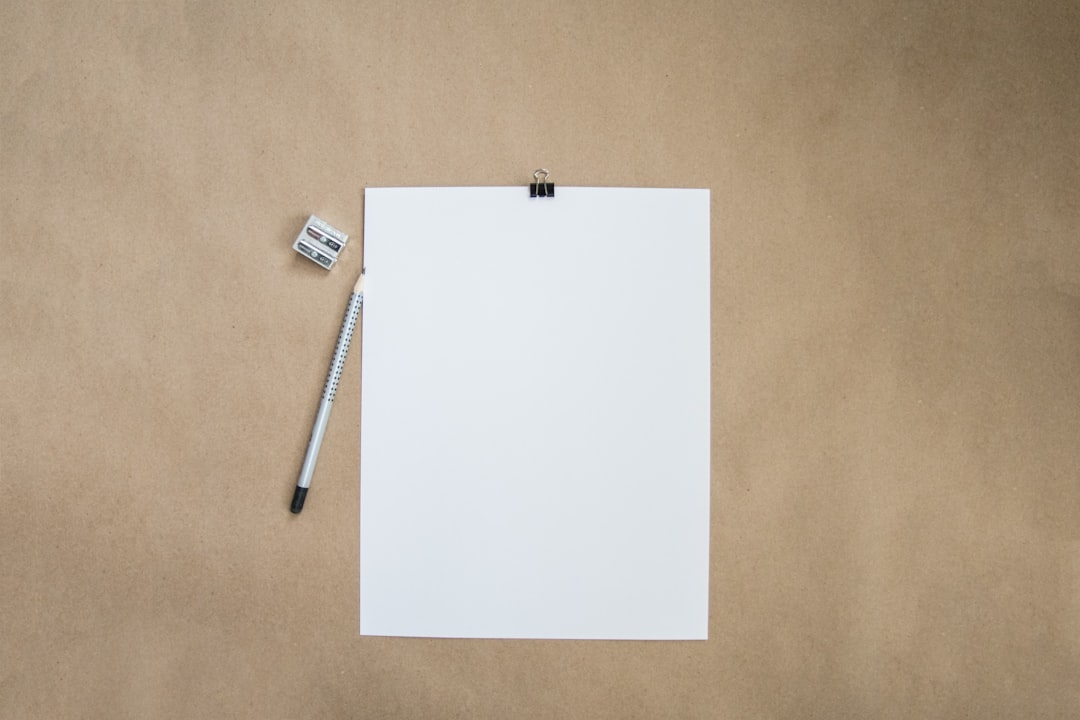
Titanium dioxide (TiO2) plays a crucial role in enhancing the visual appeal and functionality of paper. Its primary function is to boost the paper's brightness and opacity, making printed content stand out more vividly. This ability stems from its high refractive index and excellent light-scattering properties, which allow it to reflect and scatter light effectively. The result is paper with a whiter appearance and a reduced tendency to allow light to pass through, improving the overall print quality, especially for text and images.
Moreover, TiO2 offers a degree of UV protection, safeguarding the paper from the damaging effects of sunlight and extending its lifespan. It also provides a degree of durability, which allows for the use of less material to achieve the desired paper strength and thickness, streamlining manufacturing processes and potentially reducing overall costs.
Recent research into TiO2 focuses on nanostructured composites that appear to enhance the already impressive brightness and opacity of the paper. These advancements could lead to a new generation of paper with superior optical properties, opening possibilities for higher-quality prints in various applications. However, it's important to consider the long-term implications of using TiO2 in large quantities and the ongoing need to explore more sustainable and environmentally friendly alternatives for future paper production.
Titanium dioxide (TiO2) is a widely used additive in papermaking, primarily due to its remarkable ability to scatter light. This property significantly enhances the whiteness and opacity of paper, making it ideal for applications demanding vibrant colors and high-quality print reproduction. The way TiO2 interacts with light is fascinating, as its high refractive index allows for the use of finer particles in coatings. This leads to a smoother paper surface, which is crucial for optimal ink transfer during printing, minimizing issues like ink bleed and feathering.
Beyond its visual enhancement, TiO2 also acts as a UV stabilizer, protecting paper from the damaging effects of ultraviolet light. This is particularly relevant for extending the lifespan of printed materials exposed to sunlight or artificial light sources. However, the performance of TiO2 can depend on its crystalline form. For example, the anatase form often shows better performance in paper coatings compared to the rutile form, indicating that selecting the right TiO2 type is vital for achieving desired results.
While TiO2 offers numerous benefits, its use in paper coatings also presents some interesting challenges. For instance, TiO2's tendency to flocculate, or clump together, can lead to inconsistencies in coating application, potentially impacting print quality. Understanding and managing this behavior is crucial for maintaining consistent coating uniformity and, subsequently, printing outcomes.
Moreover, the interaction of TiO2 with other additives in coating formulations is complex. For instance, combining TiO2 with polymeric binders can enhance both adhesion and durability, improving overall performance in various printing applications. Research suggests that these combinations can also enhance moisture resistance, making the paper more suitable for applications where it might be exposed to humidity or water.
Besides improving brightness, TiO2 also plays a critical role in boosting paper opacity. This is especially important for applications like two-sided printing, where it helps to prevent show-through from one side to the other. Interestingly, TiO2's reflective properties don't just enhance whiteness, they also seem to intensify colors, making them appear more saturated and vivid. This impact on color perception is significant for applications where color accuracy and impact are important.
Finally, TiO2's influence on the surface tension of paper can optimize ink adhesion, which is crucial in high-speed printing. Reduced surface tension can lead to faster ink drying times, a critical factor for maintaining production efficiency and meeting modern printing deadlines. This property highlights the intricate interplay between TiO2, ink, and paper during the printing process, demonstrating the importance of careful consideration when selecting and implementing TiO2 in paper coatings. It's clear that TiO2 remains a valuable additive in the world of papermaking, presenting a fascinating field for continued research and exploration.
Understanding the Science Behind Paper Coatings 7 Key Differences That Impact Print Quality - Silica Gel Layers Enable Better Ink Absorption Control
Silica gel layers are gaining attention for their ability to improve how paper absorbs ink, which directly impacts the quality of printed materials. These coatings, primarily made of silica, have a structure that encourages ink to penetrate the paper more effectively. This better ink absorption can lead to more precise ink dot formation, contributing to sharper images and text.
Furthermore, the absorption rate of ink isn't just about the material itself. Introducing positively charged (cationic) components to the silica layer helps it interact more favorably with the ink's dye molecules, which are often negatively charged. This optimized interaction contributes to more controlled and efficient ink absorption.
The growing popularity of inkjet printing, particularly for producing high-quality photos, has increased the need for paper that can handle various types of inks and dry quickly. Silica-based coatings, with their ability to fine-tune ink absorption, are being explored as a solution to fulfill this demand. However, the optimal design of silica-based coatings for specific types of printing remains a complex challenge. Ongoing research and development are key to understanding how different variables like temperature, ink composition, and coating structure affect the ultimate quality of the print.
Silica gel layers are increasingly used in paper coatings, particularly for inkjet printing, because of their ability to finely tune ink absorption. This control is crucial for print quality, as it minimizes issues like ink bleeding and feathering, which can blur printed images and text. The way silica gel interacts with the paper surface is intriguing, as it seems to alter the surface energy, making the paper more receptive to ink. This enhanced wettability helps promote better adhesion and more even distribution of ink during printing.
One particularly interesting feature of silica gel is its ability to absorb and release moisture. This property can help regulate humidity levels within the paper, which is important for preserving the structural integrity of printed materials and preventing warping or curling. The size of the silica particles within the layer also appears to play a role in print quality. Smaller particles tend to create a more uniform and smoother surface, potentially leading to sharper print details and higher resolution images.
The thickness of the silica layer can also be adjusted to fine-tune printing outcomes. Thinner layers might be favored for faster drying times, while thicker layers can provide more ink holdout, resulting in more vibrant and intense colors. However, similar to latex coatings, silica's behavior can be influenced by temperature. This sensitivity likely impacts the interaction of silica with the ink and water, potentially affecting drying rates and ink absorption.
Silica layers can be combined with other types of coatings, leading to potentially synergistic effects. For instance, pairing silica with polymer binders might create a surface that is both durable and offers exceptional print clarity. Furthermore, silica gel can affect the overall visual characteristics of the paper by scattering light. This could contribute to improved brightness and potentially a more vivid and impactful print.
Unlike certain organic coating components, silica is highly chemically stable. This stability translates to longer-lasting print quality and less degradation over time. Interestingly, silica gel coatings may also enhance the bonding strength between the paper fibers and the coating layer. This increased adhesion results in a tougher, more durable paper surface, which is beneficial for withstanding various printing techniques. It seems that silica layers can positively impact a wide range of print characteristics through its unique interactions with ink and the paper substrate, offering a valuable tool in optimizing print quality.
Understanding the Science Behind Paper Coatings 7 Key Differences That Impact Print Quality - Polyvinyl Alcohol Films Create Distinct Gloss Variations
Polyvinyl alcohol (PVA) films are increasingly recognized for their ability to generate distinct gloss levels in paper coatings. This capability stems from their inherent smoothness and the manner in which they interact with and fill gaps between the paper fibers. Their versatility is enhanced by the possibility of blending PVA with natural materials, leading to a range of performance characteristics. This adaptability makes PVA films promising for applications where both aesthetics and functionality are crucial, including enhancing the surface properties of paper and improving its barrier properties against moisture and other environmental elements. The potential of PVA coatings also aligns with the growing demand for more sustainable and eco-friendly paper production processes, moving away from traditional, less environmentally sound materials. However, while PVA demonstrates promising potential, there's a need for a continued understanding of how its various formulations influence print outcomes in the practical applications of paper production and printing. The ongoing research in this field is crucial to optimize the use of PVA films for various printing needs and to ensure the consistency of their effects on gloss and other relevant attributes.
Polyvinyl alcohol (PVA), a polymer often used in various industries, including paper coatings, presents intriguing possibilities for controlling the gloss of paper surfaces. The degree of gloss achieved with PVA films seems to depend on several factors, including the smoothness of the resulting film and the extent to which the film fills the gaps between paper fibers. This creates a fascinating opportunity for influencing the visual appeal of printed materials by adjusting the PVA coating process. It's still unclear exactly how these factors interact and how precisely the gloss can be controlled, making it a subject for ongoing exploration.
PVA's mechanical properties also offer a level of versatility that may prove advantageous in printing applications. The tensile strength and flexibility of the film can be altered during the formulation process simply by changing the concentration of the PVA. This allows for the tailoring of the coating to withstand the rigors of different printing methods and end-use requirements, an area that requires further study.
The surface chemistry of PVA films, in relation to the inks used in printing, presents another area of potential control over print quality. Depending on how the PVA is applied and cured, the ink interaction with the coated surface can either enhance ink absorption or reduce ink bleed. This flexibility is important for optimizing ink performance and achieving the desired results in various printing techniques. It would be interesting to understand how to best manipulate this aspect of the coating process.
A noteworthy attribute of PVA coatings is their water solubility. This property, though simple, can provide valuable functionalities in some applications, as it allows for easier removal of the coating when needed. This could be beneficial in processes where temporary adhesion or protection is desired, but more research is needed to understand how this aspect can be most effectively incorporated into diverse printing scenarios.
PVA films display a specific sensitivity to temperature, as they soften and deform when heated. This characteristic potentially enables innovative post-processing methods such as thermal lamination for enhanced print finishes. Further studies are needed to understand how precisely this feature can be used to enhance various aspects of print quality, such as gloss and durability.
When employed alongside other coatings, PVA can act as an intermolecular adhesive, contributing to stronger bonds and enhanced durability of the overall coating. The exact nature of how PVA interacts with other types of polymers and the specific resulting improvements in performance characteristics is an active area of research.
Interestingly, the degree of gloss achieved with PVA appears to be linked to the underlying changes in the paper surface's texture. This means that, by manipulating the PVA coating process, both the gloss level and the surface texture of the paper can be specifically targeted for unique visual effects in printed materials. While the exact mechanisms are not yet fully understood, this connection presents a valuable avenue for exploration in tailoring the printing process.
Environmental humidity also plays a role in the behavior of PVA coatings, an aspect that might cause challenges in certain conditions. As PVA coatings can be sensitive to variations in humidity, maintaining a consistent printing environment is crucial to ensuring predictable outcomes and consistent print quality. A greater understanding of these sensitivities is important in various industrial settings.
The capability of tailoring PVA coatings further through the addition of other components presents possibilities for fine-tuning specific properties such as water resistance and gloss. This customization is vital for aligning coating properties with the specific needs of various printing technologies and their associated end-use applications. More work needs to be done to determine the full potential of these custom formulations.
Finally, the chemical modification of PVA, often termed crosslinking, can have significant effects on the film's characteristics. Introducing crosslinking agents can dramatically alter the film's mechanical and thermal properties, potentially increasing strength and gloss retention. This is a potentially promising area of development, especially for printing applications where a robust and glossy coating is required. However, much more investigation is necessary to understand the optimal use of these crosslinking processes in various print-related scenarios. In conclusion, while PVA coatings offer several potential advantages in terms of achieving unique gloss variations and adaptable mechanical properties, further research is needed to optimize and fully understand their application across the diverse range of printing methods.
More Posts from storywriter.pro: